-
-
REFITTING THE FRONT WHEEL
TORQUE WRENCH SETTINGS
Pinch bolt (1) 12 Nm (1.2 kgm)
Wheel spindle 40 Nm (4.0 kgm)
Screws (2) 25 Nm (2.5 kgm)
-
Position the wheel between the fork legs.
-
Locate the speedometer drive to the wheel.


-
Smear a light coat of grease over the total length of the wheel
spindle, see 1.8.1.
-
Tighten the wheel spindle from the right side.
-
Tighten the pinch bolt (1). 

-
Position the brake calliper to the brake disc.
-
Tighten the two screws (2).
-
REAR WHEEL
-
REAR WHEEL DIAGRAM

Key:
-
Complete wheel
-
Circlip
-
Bearing
-
Brake calliper and silencer carrier
-
Nut
-
REAR WHEEL REMOVAL
TORQUE WRENCH SETTINGS
Screw (1) 25 Nm (2.5 kgm)
Wheel spindle nut 110 Nm (11.0 kgm)


-
Remove the exhaust, 1.8.1.
-
Remove the rear mudguard, 7.1.15.

-
Remove the rear brake calliper but leave it connected to the hose, 7.7.5.
-
Release and remove the screw (1).
-
Remove the split pin from the wheel spindle. 
-
Remove the nut cap. 

-
Release and remove the wheel spindle nut.
-
Remove the silencer carrier.

-
Remove the shim (2) fitted to the wheel spindle.
-
Remove the rear wheel.
-
BRAKES
-
BRAKES DIAGRAM

Key:
-
Front brake lever
-
Front brake master cylinder/fluid reservoir
-
Front brake lever to calliper hose
-
Proportioning valve
-
Front brake calliper
-
Front brake pads
-
Proportioning valve to front brake calliper hose
-
Proportioning valve to rear brake calliper hose
-
Rear brake calliper
-
Rear brake pads
-
Rear brake lever to proportioning valve hose
-
Rear brake lever
-
Rear brake master cylinder/fluid reservoir

-
REPLACING THE FRONT BRAKE PADS
TORQUE WRENCH SETTINGS
Bolts (1) 25 Nm (2.5 kgm)
-
Place the vehicle on the centre stand.
-
Release and remove the two bolts (1).
-
Push the brake calliper pistons fully open, tilt the calliper
outwards and ease it off the brake disc. Proceed carefully to avoid
damaging the wheel rim (some adhesive tape may help protect the
rim).
-
Release and remove the grub screw (2).
-
Release and remove the pin (3). 

-
Extract the brake pads.
WARNING
Do not operate the brake lever with the brake
pads removed, or the brake calliper pistons might fall out leading
to loss of brake fluid.
WARNING
The brake pads must always be replaced in
pairs. Ensure they become properly seated in the brake calliper.
-
Fit two new brake pads.
-
Tighten the pin (3).
-
Tighten the grub screw (2).
-
Locate the brake calliper to the brake disc.
-
Tighten the two bolts (1).

-
FRONT BRAKE DISC INSPECTION
NOTE These
procedures must be performed with the brake disc
installed to the wheel.
-
Check for wear measuring disc thickness with a micrometer gauge at
different positions around the disc. When a disc is worn beyond the
service limit even at just one position, the disc must be replaced.
Disc thickness limit: 4.5 mm.

-
Check for disc run-out using a dial gauge. Replace disc when the
maximum run-out measured exceeds the disc run-out limit, see 7.7.4.
Disc run-out limit: 0.3 mm.
-
FRONT BRAKE DISC REMOVAL

-
Remove the front wheel, 7.5.2 .
-
Release and remove the five brake disc screws (1).
NOTE To
refit, start all screws (1) manually in their holes and tighten in a
cross pattern.
WARNING
Apply LOCTITE 270 to the threads of the brake
disc screws (1) on assembly.
-
Remove the brake disc.

-
REPLACING THE REAR BRAKE PADS
TORQUE WRENCH SETTINGS
Bolts (1) 25 Nm (2.5 kgm)
-
Release and remove the two bolts (1).
-
Remove the brake calliper from the disc.

-
Remove the retaining ring (2).
-
Withdraw the pin (3).
-
Remove the clip (4).
-
Extract the brake pads (5) one by one.
WARNING
Do not operate the brake lever with the brake
pads removed, or the brake calliper pistons might fall out leading
to loss of brake fluid.
-
Change the brake pads (5).
WARNING
The brake pads must always be replaced in
pairs. Ensure they become properly seated in the brake calliper.
-
Fit two new brake pads.
-
Insert the clip (4) in the correct position.
-
Insert the pin (3).

-
Fit the retaining ring (2).
-
Check brake fluid level, 2.10.1.

-
REAR BRAKE DISC INSPECTION
NOTE These
procedures must be performed with the brake disc
installed to the wheel.
-
Check for wear measuring disc thickness with a micrometer gauge at
different positions around the disc.

NOTE When
a disc is worn beyond the service limit even at just one position,
the disc must be replaced, see 7.7.7.
Disc thickness limit: 4.5 mm.

-
Check for disc run-out using a dial gauge. Replace disc when the
maximum run-out measured exceeds the disc run-out limit, see 7.7.7.
Disc run-out limit: 0.3 mm.
-
REAR BRAKE DISC REMOVAL

-
Remove the rear wheel, 7.5.2.
-
Release and remove the three brake disc screws (1).
NOTE To
refit, start all screws (1) manually in their holes and tighten in a
cross pattern.
WARNING
Apply LOCTITE 270 to the threads of the brake
disc screws (1) on assembly.
-
Remove the brake disc.

-
PROPORTIONING VALVE REMOVAL
TORQUE WRENCH SETTINGS
Screws (2) 10 Nm (1.0 kgm)

-
Remove the dashboard, 7.2.6.
-
Drain the brake circuit, 2.10.2.
-
Release and remove the two screws (1) and the drain valve. Collect
the seals.
NOTE Mark
the brake hoses with their position to avoid confusing them on
assembly.
-
Disconnect the three brake hoses. Block off the hose ends to avoid
loss of brake fluid.
-
Release and remove the two retaining screws (2) of the proportioning
valve.
-
Remove the proportioning valve.

NOTE Bleed
the brake circuit on refitting, 2.10.4.

-
HEADSTOCK
-
HEADSTOCK REMOVAL TORQUE
WRENCH SETTINGS
Locknut (1) 110 Nm (11.0 kgm)
-
Place the vehicle on a lift with the front wheel protruding over the
lift edge. Put the vehicle on the centre stand.

-
Place a support underneath the frame.
-
Remove the handlebar, 7.4.1.
-
Remove the dashboard, 7.2.6.

-
Remove the legshield, 7.1.9.
-
Remove the brake calliper from the disc, 7.7.2.

-
Release and remove the locknut (1).
-
Release and remove the nut (2).

NOTE Pay
attention to the lower bearing balls during front fork removal.
-
Remove the front fork together with the wheel from the steering
tube.

-
Remove the plastic seal (3).
-
Remove the rotary race (4) and the balls (5) of the upper bearing.
-
Remove the rotary race (6) and the balls of the lower bearing (7).
-
Clean off all grease from the bearing components, including the
fixed races (8) and (9).
-
Remove the dust seal (10).
-
Check all components for wear and replace as required.

NOTE 1.8.1.for
the specified bearing grease.
-
Refit all components and adjust play in the bearings.

-
COMPONENT INSPECTION
WARNING
Ensure that all components are in good
condition.
Check the contact areas of the balls (1) on the rotary (2) and fixed
(3) races for damage or wear. Replace the complete bearing if any
component is damaged or worn.
WARNING

Grease the contact areas of the balls in both
races (2-3), 1.8.1.
-
FRONT FORK
-
FRONT FORK DIAGRAM

Key:
-
Steering stem and bottom yoke
-
Fork clamp bolts
-
Retaining ring
-
Rubber cap
-
Sealing cap
-
O-ring
-
Spring
-
Damping cylinder
-
Counter spring
-
Centring bush
-
Left slider
-
Dust seal
-
Retaining ring
-
Seal
-
Retainer
-
Bush
-
Left stanchion tube
-
Sealing washer
-
Capscrew
-
Right slider
-
Right stanchion tube
-
Pinch bolt

-
REMOVING THE STANCHION TUBES AND SLIDERS
NOTE The
procedures described below apply to both fork legs.

-
Remove the front wheel, 7.5.2.
-
Remove the front mudguard, 7.1.14.
-
Release and remove the two bolts (1).

-
Remove the upper retaining ring (2).
-
Remove the stanchion tube and slider assembly.

-
DISASSEMBLING THE STANCHION TUBES AND SLIDERS

-
Drain all oil, 7.9.4.
-
Place the fork leg in a vice with soft (aluminium) jaws.
-
Release and remove the capscrew (1). 

-
Remove the slider and collect the centring bush.
NOTE Proceed
carefully when removing the different components, or you might
damage the inner seating surface of the slider.

-
Remove damping cylinder (2) and spring (3) from the slider.
-
Prise the dust seal off the stanchion. 
-
Prise out the retaining ring. 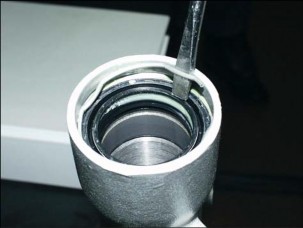
-
Remove the oil seal. 

-
Remove the washer.

-
Remove the shim (4) if needed.

-
DRAINING THE FRONT FORK

NOTE Make
sure to have a container having a capacity greater than, 1.7.1.,
ready at hand before proceeding.
-
Place the slider in a vice with soft (aluminium) jaws.
WARNING
The stanchion-and-slider assembly contains
oil. Do not turn it over or tilt it during removal.
-
Remove the top cap. 

-
Push down the damping cylinder just enough to give access to the
retaining ring (1).
-
Remove the retaining ring (1).

-
Raise the spring and allow some time before extracting it to let oil
drip back into the slider.

-
Drain oil into the container. Pump the slider back and forth to
facilitate draining.

-
FILLING THE FORK
-
Place the stanchion-and-slider assembly in a vice with soft
(aluminium) jaws.
-
Insert the spring. 

-
Pour oil into the fork.
WARNING
Never reuse the oil you have drained
previously.

-
Insert the top cap complete with O-ring.
-
Insert the damping cylinder (1). 

-
Push down the damping cylinder until exposing the retaining ring (2)
groove.
-
Insert the retaining ring (2).

-
Fit the top cap.

-
COMPONENT INSPECTION Read 1.2.1. carefully.
STANCHION TUBE
-
Inspect the sliding surface for scoring and/or scratching. Eliminate
minor scoring with wet sand paper (grain size 1).
-
Replace the stanchion if badly scored.
-
Check for stanchion buckling using a dial gauge.
-
Replace the stanchion if buckled beyond the service limit.
Service limit: 0.2 mm.
DANGER
NEVER attempt to straighten a buckled
stanchion as this would weaken the overall structure leading to a
dangerous riding condition.

SLIDER
-
Inspect for damage and/or cracking. Replace if damaged.
-
Change any component which is badly worn or damaged.
Renew the following components on assembly:
-
top cap O-ring (1);

-
oil seal (2);
-
dust seal (3);
