-
Before reassembling the carburetor, thoroughly clean carburetor
body with fuel and compressed air.
-
Take special care to the fuel delivery line and to the metering
rod location.
-
Accurately check full-power circuit air calibration.
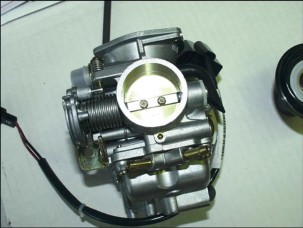
-
As for the idling circuit, make sure that the following parts
are perfectly clean: air calibration, outfeed section
managed by the flow adjuster screw, progression
holes at the throttle.
NOTE The
idling air of the 200 cc version is controlled by two
calibrations. The cut-off calibration is directly
derived from
the carburetor body.

-
Check that the five closing balls of the working ducts are
positioned on the carburetor body.
-
Check that the surface mating float chamber and membrane
are not dent.
-
Check that the vacuum valve duct is not scored.
-
Check that the throttle valve and shaft are not excessively
worn.
-
Check that the metering rod location is not excessively worn.
-
If this is the case, change the carburetor.
NOTE To
avoid any damage, do not insert metal parts into the
gauged sections.

-
Thoroughly wash and blow idling jet (1). Refit.
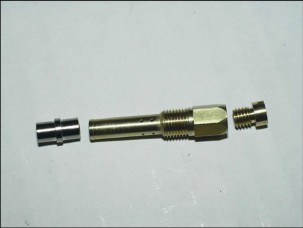
-
Thoroughly wash and blow spray nozzle full-power circuit,
diffuser and jet.
-
Install the spray nozzle into the carburetor body. Make sure
that the cylindrical side, which is shorter, is facing the
diffuser.
-
Fit the diffuser. Make sure that the spray nozzle is properly
positioned. Lock in place.
-
Fit the full-power jet.

-
Check that the surface of the tapered metering rod mating
the dampened pin and the return spring is not worn.
-
In case of wear, change the metering rod.
-
Check that the float surface at the pin location or at
the metering
rod contact plate is not worn. Check also for fuel
leaks.
-
In case of malfunctioning, change the parts.
-
To fit the float with metering rod, insert the pin from
the fuel
feeding side.
NOTE Take
care that the return spring is correctly installed into
the float plate.
CHECKING THE LEVEL
-
With the carburetor in upside-down position, make sure that
the float mating surface is parallel to the float chamber
surface.
-
If this is not the case, change the metering rod metal plate
direction until reaching the above position.
-
If the plate shape is changed, make sure that it is
still parallel
to the float pin.
NOTE With
the carburetor in upside-down position, the float weight
should not counteract the tapered metering rod spring thrust.
If this is not the case, check that the float is free
from fuel.
Change the float and the tapered metering rod, if necessary.

-
Thoroughly wash and blow the fuel conveyor cap (2) and
fit it onto the starter.
NOTE Failure
to fit this part leads to a worse cold starting, since
the starter jet takes old fuel from the float chamber bottom.

-
Remove the float chamber exhaust screw (3), thoroughly
wash and blow the float chamber. Make sure
to perfectly clean the pick-up pump intake and delivery
valve.
-
As these are one-way valves, gently blow with compressed
air into the intake valve working from the float
chamber inner side and into the exhaust valve working
from the pump piston seat.

-
Check the pick-up pump piston and its seat into the float
chamber for wear.
-
If this is the case, change the worn parts.
-
Check the pick-up pump piston return spring for wear.
-
Fit a new OR-seal and a new bellows seal. Refit the piston
unit onto the float chamber.
-
Fit a new OR-seal in the float chamber exhaust screw. Tighten
the screw.

-
To check screw proper sealing, pour a small quantity of fuel
into the float chamber.
-
Fit a new seal on the float chamber.
-
Fit the float chamber to the carburetor body. Tighten the
four screws.
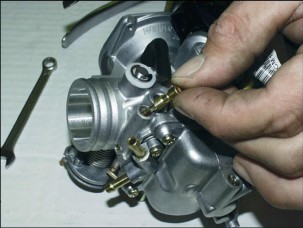
-
Thoroughly wash and blow the flow adjuster screw. Fit a
new OR-seal.
-
Pre-assemble the following parts on the screw in the following
order: spring, washer and OR-seal.
-
Screw the flow screw on the carburetor body.
-
Screw final position will have to be defined according to
the exhaust gases analysis.
-
Prepare carburetor for adjustment by loosening the screw
by three turns starting from the closed position.
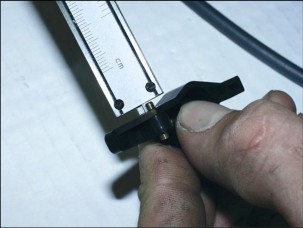
-
Check that the pick-up pump control rocker arm is not excessively
worn.
-
Check that the rocker arm set screw juts of:
-
125 cc engine: 3.7 mm
-
200 cc engine: 3.2 mm.
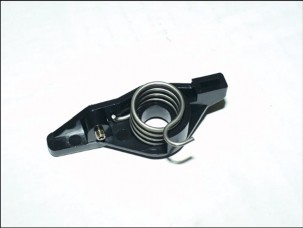
-
Check the rocker arm return spring for yielding.
-
Pre-assemble spring and rocker arm.
-
Keep the throttle open and fit the rocker arm on the carburetor.
-
Tighten rocker arm screw.
-
Make sure that the mechanism works properly.

CHECKING THE VACUUM VALVE AND THE TAPERED METERING
ROD
-
Undo the bayonet-coupling by 1/8th of
a turn and remove
it. Remove spring and vacuum valve metering rod.
-
Check the metering rod for wear and that the retainer is
positioned inside the third notch.
-
Check the outer diameter vacuum valve for scoring.
-
Check that the two vacuum feeding holes are not obstructed.
NOTE The
2 holes have different diameters.

-
Make sure that the membrane is not broken or hardened.
If this is the case, change it.
-
Refit the tapered metering rod on the vacuum valve.
-
Make sure that the spring is correctly positioned on the metering
rod and that coupling is perfectly seated.
-
To fit the coupling, turn it by 1/8th of
a turn.
-
Refit the vacuum valve on the carburetor. Make sure that
the tapered metering rod seats into the spray nozzle.
-
To time vacuum valve rotation, insert membrane end into
its location. The membrane is correctly fitted to the valve
when vacuum main feeding hole is in axialposition
with the choke tube, on the throttle side (see figure).
-
Refit spring onto valve.
-
To refit vacuum chamber cover, make sure that the reference
on cover matches with that on the membrane.
-
Tighten screws to the specified torque.
-
Check for cut-off valve proper positioning, for 200 cc version
only. Check that the membrane is not broken or
hardened. Check spring free length.
Standard length: 24 mm
-
Refit membrane with the metal pin on valve. Refit spring
and cover. Make sure that cover vacuum port is facing
upwards.
-
Wash and blow starter mount.
-
Refit a new seal on carburetor body and tighten the two
fastening screws.
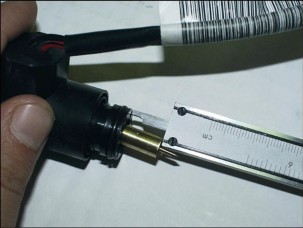